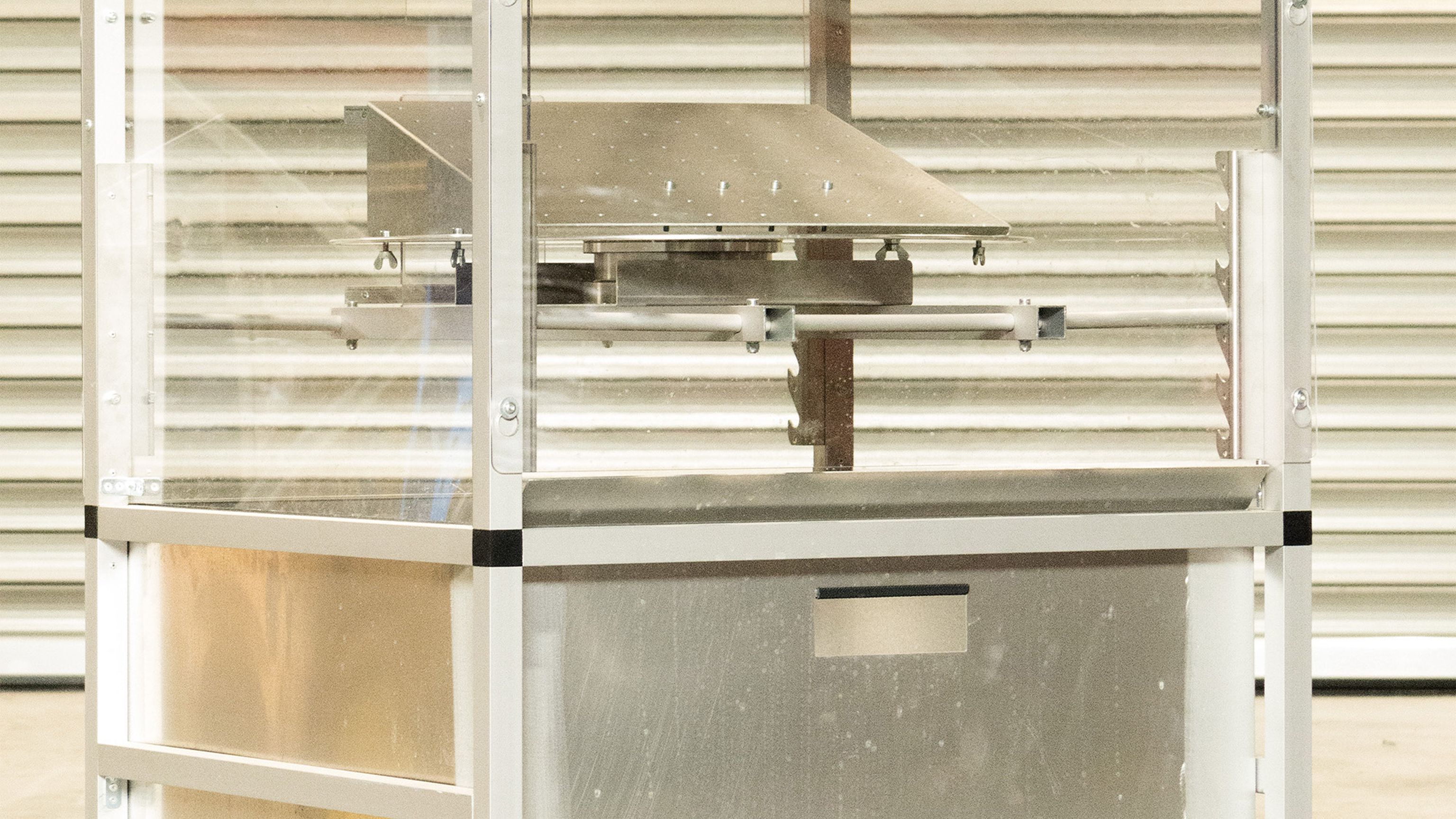
Product tests during development
The sustainability of a product is often only defined by the life cycle assessment of a material or its manufacturing technology. However, the functional reliability and therefore the longevity of a product - whether it is only in use for around 3 years or 15 years - is an equally important factor for the sustainability of a product. Extensive validation of a product during the development process is a very important part of this.
In recent years, many manufacturers have significantly reduced the amount of time spent on validation and verification in the product development process. This is due to ever shorter development processes and, in some cases, shorter product life cycles and a larger number of product variants. On the other hand, however, the complexity of the products and their functional requirements and miniaturization have mostly increased, which would actually result in a greater proportion of validation.
In our view, it is therefore all the more important to obtain initial indications of essential product functions as early as possible during the development process. It is true that many things can now be simulated in computer programs. However, any simulation is only as good as the data and formulas on which it is based.
However, especially when it comes to dynamic stresses and the impermeability of products, the simulation effort is usually quite high and can often only represent a part of the later real load.
We at BUSSE therefore try to proactively support our customers in this area and for this reason have developed and built simple test devices for validating drop tests (shock absorption) and water resistance (IP protection class). This test equipment enables us to practically record the first important indications at an early stage, e.g. with functional samples, and incorporate them into the design.
The drop tests use RP models or models milled from the original material to demonstrate relatively clearly which areas are subject to the greatest stress and how the components shift in relation to each other. Optimized versions can then be tested in the same way and often lead to important additional findings, as the kinetic energy after stiffening one point is often transmitted to another point - ideally distributed over several functional elements.
Initial samples can also be tested in the same test setup and the behavior can be compared with the tests carried out during development. This provides important information, especially when using recycled materials or changing materials during the production process.
The IP protection class is in turn of great importance for almost all electronic products in order to protect the circuit boards themselves from short circuits caused by water bridges between live components and to protect the user from uncontrolled electric shocks. A high degree of flexibility in the test equipment was important to us in order to cover as many requirements as possible while remaining as close as possible to the standard specifications. We have therefore created a simple test chamber. This allows irrigation from several sides according to the IP classification.
For many customer projects, we have created additional project-accompanying test devices (e.g. drawer pull-out test or conveyor system test benches) to simulate the behavior under continuous load and the wear effects over the entire life cycle.
Of course, these test devices cannot be compared with those of accredited testing institutes, but they offer us and our customers a quick and cost-effective way of gaining practical knowledge and initial validations at an early stage and incorporating them into the development process.
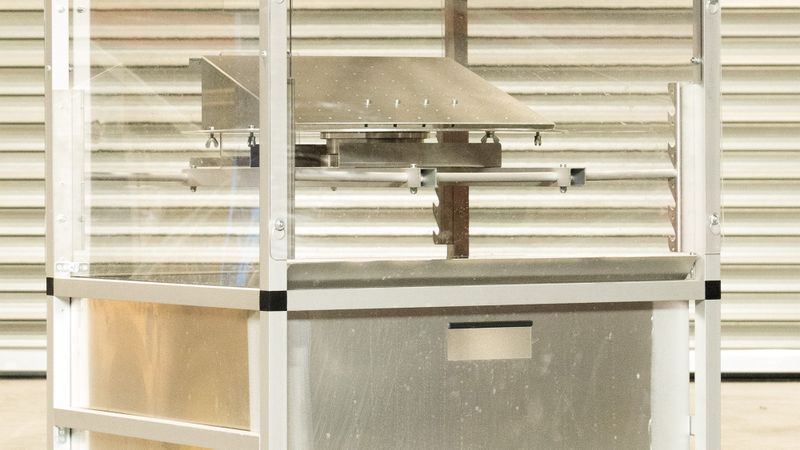
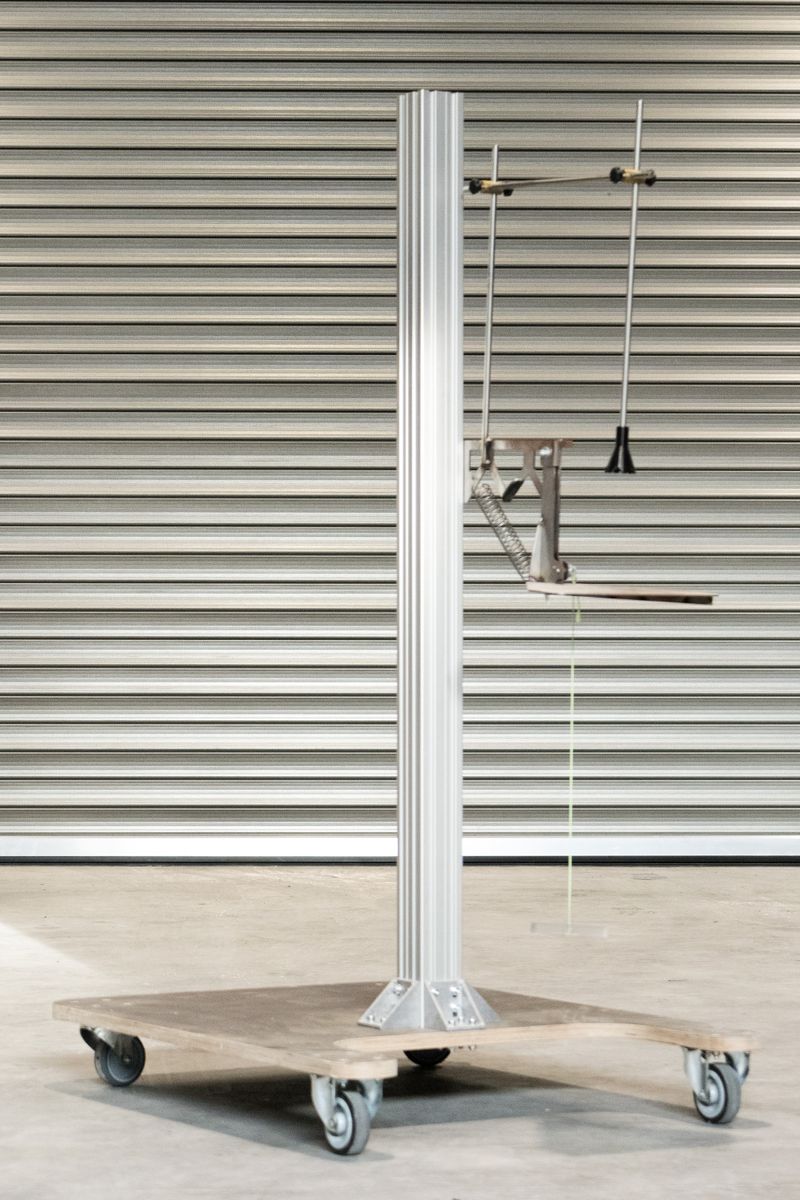
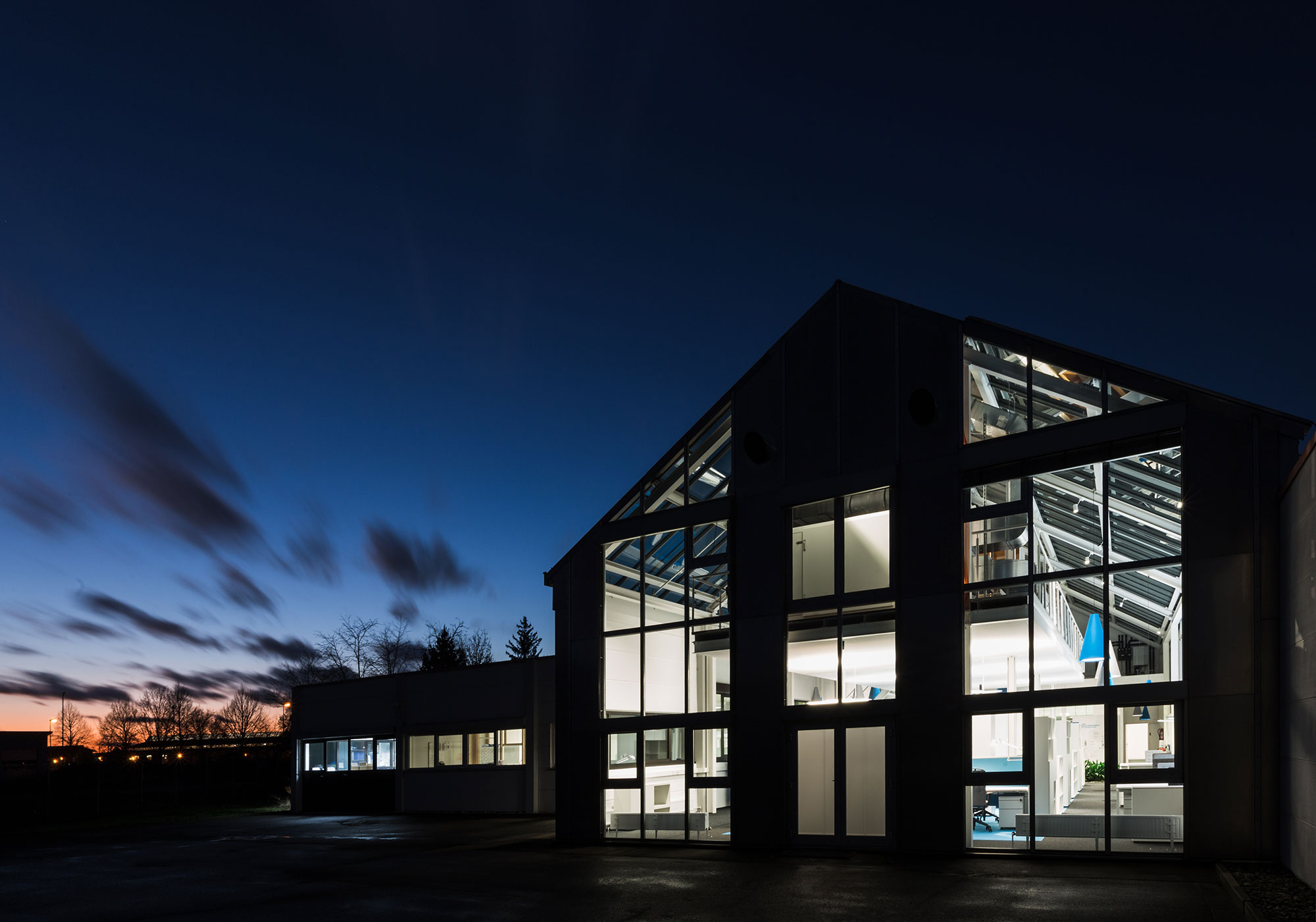