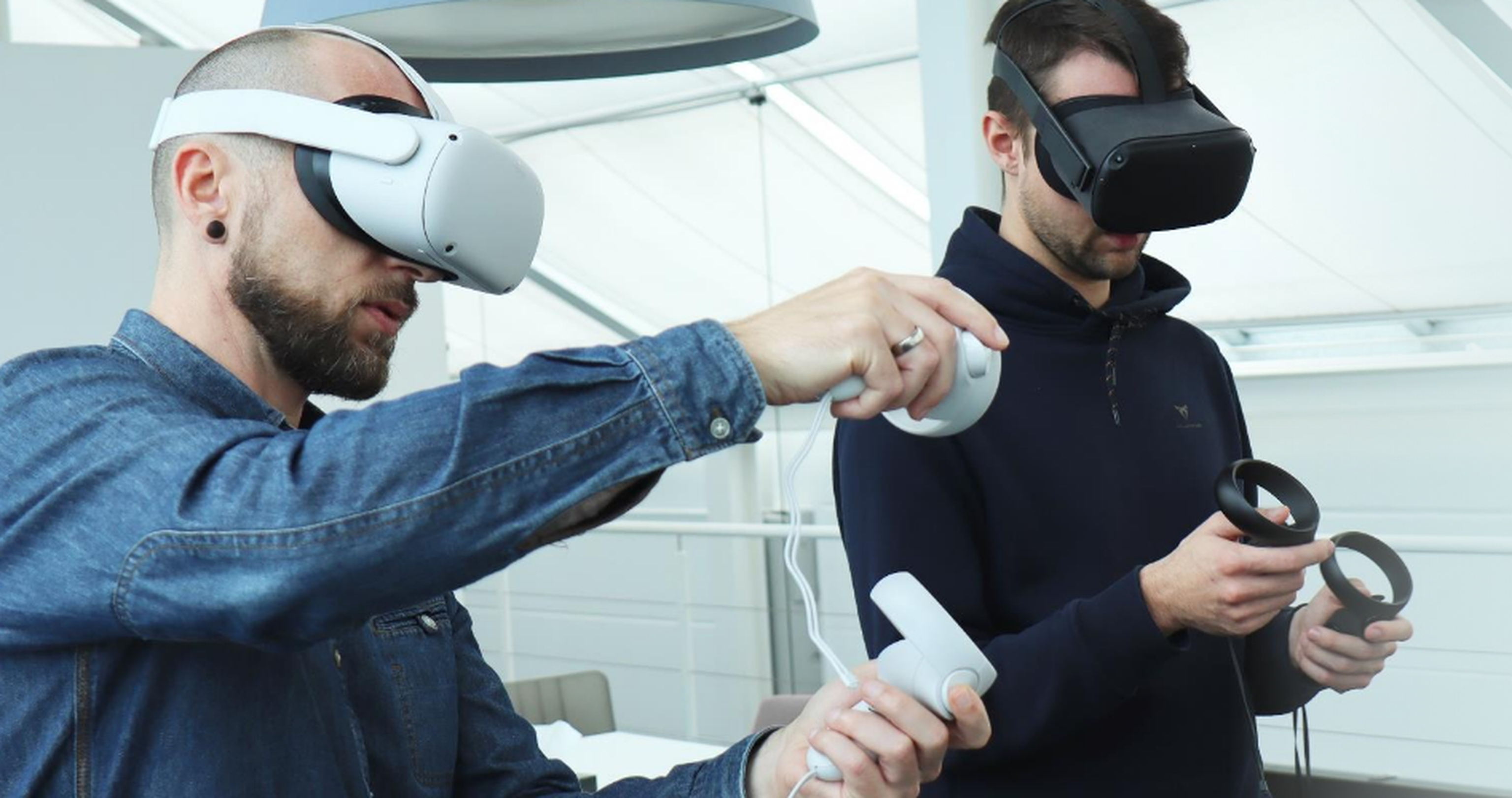
VR/AR in product development
VR and AR in the design process
A decisive moment in product development is the evaluation of ergonomics, usability, design and feasibility. Digital operating concepts can be tested using click dummies, while physical products can be evaluated using design or ergonomics models. But what if both need to be combined and optimized? Model construction enables different setups, but drives up costs with each variant. This is where we rely on smart, resource-saving solutions.
Even in the early concept phase, we use three-dimensional space to virtually “sketch” design ideas and coordinate them closely with the technical package. In VR/AR, various concepts can be displayed life-size alongside competitors and predecessor products. Although this 3D data is not parametric, it can be imported into CAD programs as a reference or used for initial RP models.
AR/VR as a simple visualization method
Using a combination of model making, interface design and 3D data, we can make operating concepts tangible, assessable and modifiable via hybrid augmented reality.
By building up CAD data and physical elements, e.g. consisting of a seat and steering unit in virtual reality, a wide variety of concepts for operating interfaces, such as joysticks, displays in different sizes and orientations, hard keys or control elements can also be built up and provided with digital interface design elements.
In a joint workshop, different scenarios can then be tried out using VR glasses, as all operating interfaces can be touched and moved using the 3D display.
This allows new concepts to be created with optimum ergonomics and usability. The experience of the VR glasses wearer is transmitted live to all participants via a screen or projector. This saves time and complex development loops and therefore also costs.
This approach is not only feasible for vehicle cabins, but can also be applied to any product with several conceivable user interfaces.

Your consent is required. This content is hosted by a third party (www.youtube.com). By showing the external content you accept the the terms and conditions of www.youtube.com.
Virtual Reality in the design process
To design in virtual reality, we use “Gravity Sketch” and can therefore work on a VR design with one or more people at the same time. From three-dimensional line drawings and surface models to the construction of entire usage environments (static), which can also be ergonomically tested, ideas can be developed quickly and form an optimal basis for a production-ready design.
With “Gravity Sketch”, the advantages of analog sketching and digital surface construction are directly combined:
On the one hand, as a designer, you remain very free in the early project phase, as in the two-dimensional design, and in the best sense of the word, you can work very precisely on the underlying package, so that hurdles such as your own three-dimensional imagination or the scope for interpretation of designs by external viewers are reduced to a minimum.
A further benefit of projects in which the end user plays a central role is that ergonomic components can be considered from the outset, which enriches the entire development process.
Several VR headsets can be used simultaneously in the virtual design room and a desktop version of Gravity Sketch is also available for PC-only users so that they can take part in reviews without VR hardware.
Time and again, we experience the enthusiasm of our customers when they put on the VR glasses themselves and immerse themselves in the design itself for large-scale projects or when the virtual design appears almost tangible right in front of them in the room.
Advantages of VR/AR
Augmented reality makes products almost tangible even before conventional model making - different colors and features can also be displayed and projected directly into the later environment.
The special thing about digital prototypes: AR displays the products in their original size and in the respective usage environment. Colors and material appearance as well as light and shadow effects tailored to the environment ensure that the virtual design models can be integrated as if they were close enough to touch.
With virtual models, coordination and decisions can sometimes be made much faster than with a physical prototype, as less effort is required to create them.
Of course, a virtual prototype does not completely replace the physical prototype. Although the design and size can be assessed very well with the virtual representation, AR cannot yet keep up with real prototypes in terms of haptics or ergonomics.
Our range of services
VR/AR product sketches in the design process
VR/AR product presentations
Hybrid AR models in combination with physical model making
Product renderings and animations
Interested in VR/AR in product development? Please get in touch with us! We will answer all your questions on the subject.
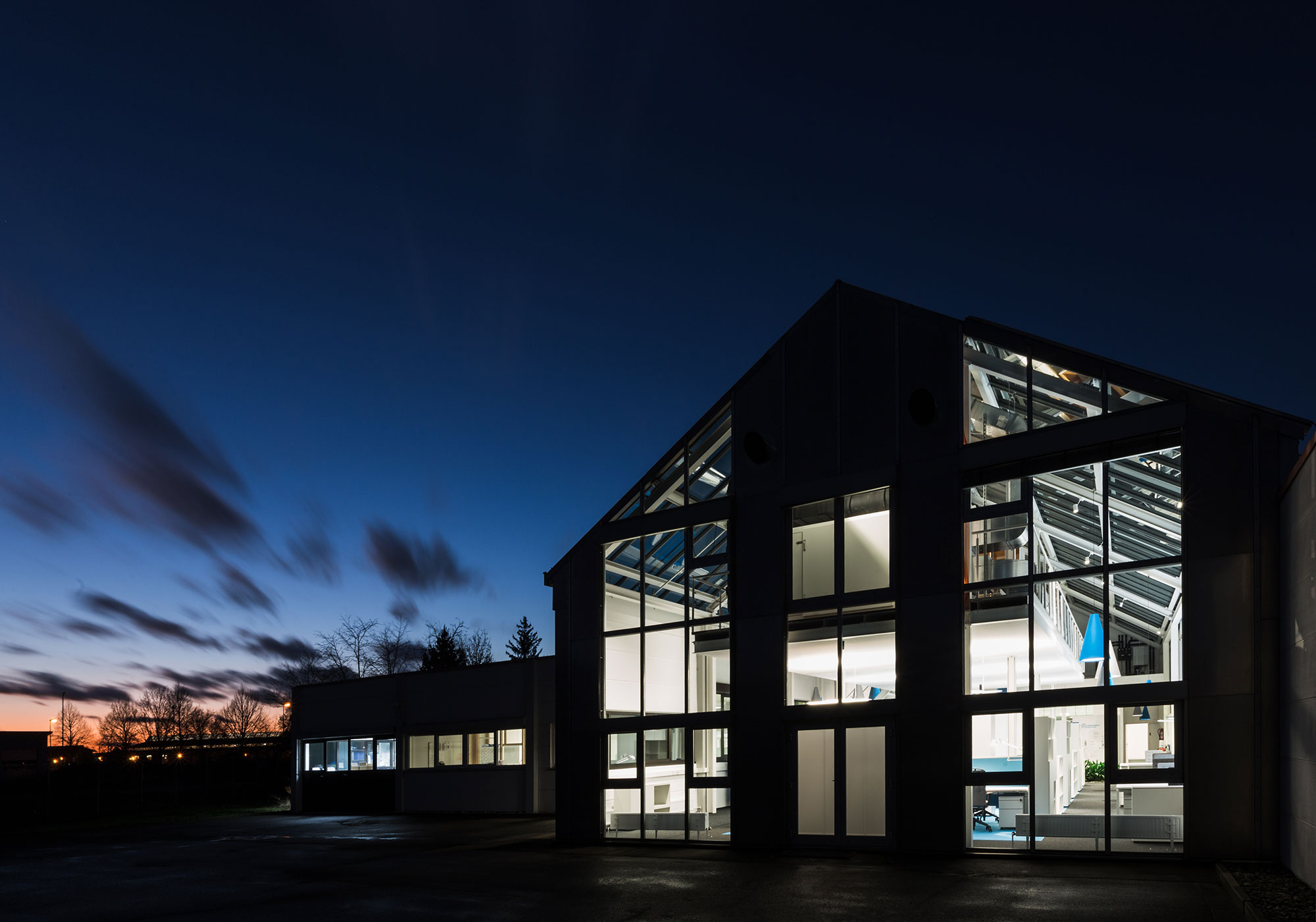