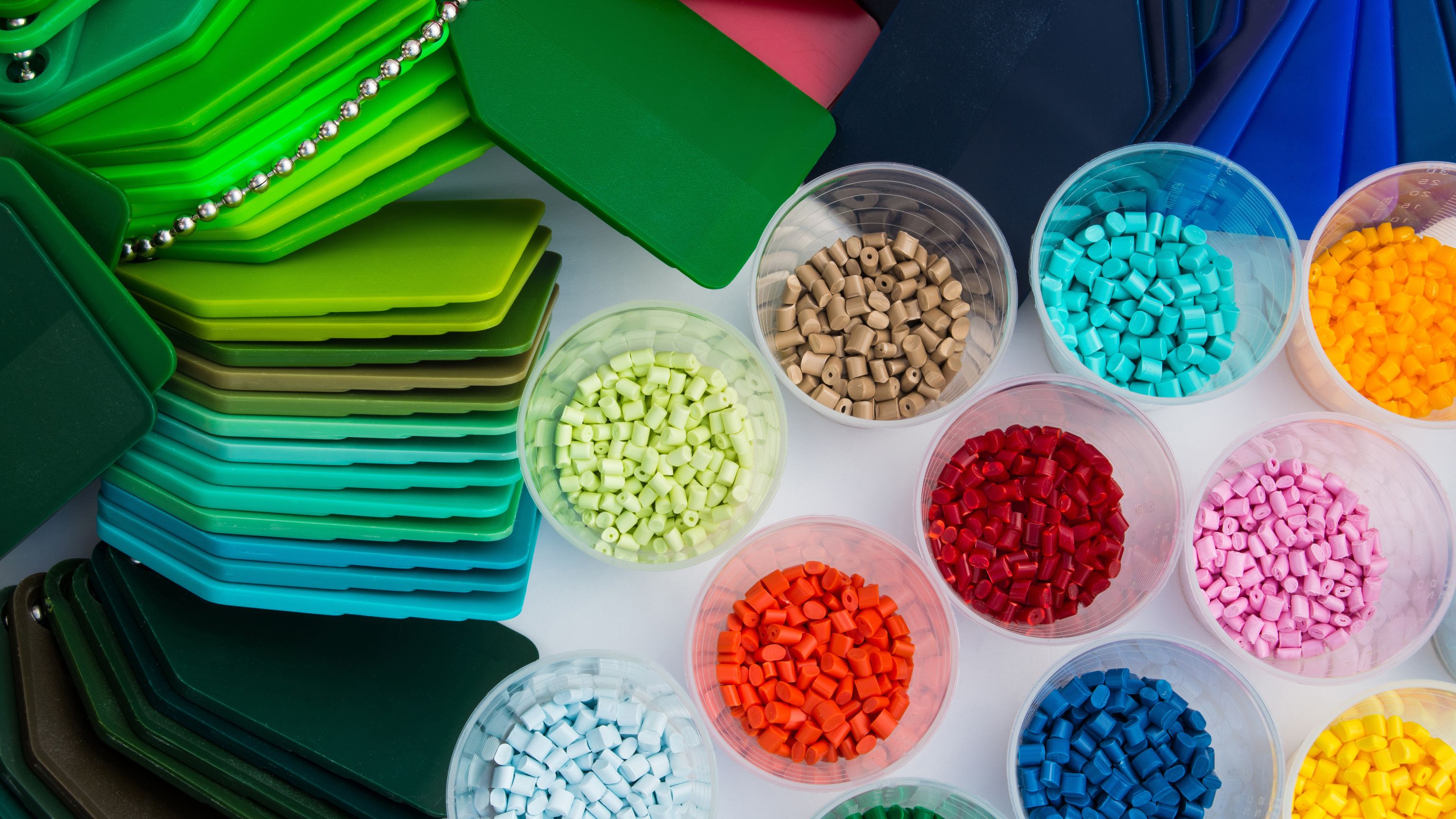
"If you know plastic, take steel" What to consider when transferring plastic parts to series production....
Plastic parts are ideal for products in large quantities and because these components can be used to create functional and structural elements as well as aesthetically pleasing outer surfaces and housings. And if they can be dismantled, repaired and designed to be durable, plastic products definitely meet the criteria of sustainability.
However, the step from the ideal CAD geometry to the finished series part is not just a matter of "pressing a button" and mapping the negative counterpart shape in steel, but involves a number of pitfalls that can lead to massive delays, quality problems, additional costs and potential conflicts and ultimately jeopardize the success of the product and project.
In order to keep these factors to a minimum during product development, an intensive exchange between the subsequent injection molding partner, the designers and toolmakers and the actual client as the subsequent distributor of the products is necessary. The essential functions and their planned use, potential misuses as well as the service life and the resulting requirements for materials, tolerances, strength and appearance should be clearly reflected, measurably defined and made clear to all parties. In addition, tests during development and later also during series production, their execution and characteristic values must be clearly specified and defined. It must also be defined which validations are to be carried out at what time (e.g. on initial samples, but also as random samples per batch) and by which party, e.g. QA of the manufacturer or the distributor.
The transfer to series production also represents a transition of responsibility between development and series production, which must be clearly defined:
Ideally, an initial round of inquiries about the most important tool-related components should be made with potential suppliers early on in the development process, so that the basic feasibility can be clarified and an initial indication of tool costs and part prices is available, and the initial feedback from suppliers can be taken into account in terms of design and the basic demolding strategy and materials can be agreed. After successful prototype testing, a clearly documented inquiry should then be made so that selected suppliers can submit comparable offers based on clearly defined criteria (e.g. demoulding strategy, tool design, cavities, slides, materials, tolerances, assembly processes, etc.). Ideally, a pre-selection for a supplier must already be made at this point, or at least a supplier should be given a specific budget for a detailed DFM assessment and ideally initial mold flow analyses.
Only on the basis of this detailed manufacturing input can the design be finalized to the extent that binding offers from suppliers are possible. If this initial DFM analysis and mold flow are not carried out, the suppliers' offers are usually based on the assumption of ideal conditions (e.g. ideal injection point, most favorable mold design with regard to cooling and demolding) and when the order is placed, either a cost-driven poorer design of the components or a frustrating cost discussion already takes place.
The injection molding supplier often makes well-intentioned recommendations from a production and cost perspective (e.g. other materials, combining components in 1+1 molds with different injection points, etc.), which must be carefully evaluated together with regard to the effects on the product and function. For example, a material that is easier to print may offer poorer strength or dimensional accuracy, which can jeopardize the overall function.
On the other hand, tolerances and fits can and should - where possible - be reduced and increased by design so that any production-related distortion of the components ideally has no or less serious functional effects on the overall function. Functional and tolerance-critical aspects as well as optical criteria must be defined, appropriate re-setting strategies and stock dimensions agreed and these taken into account during initial sampling and with regard to tool correction times. Additional components are often installed in the plastic parts, which also have their own tolerances and further tighten the requirements for the components - this must also be taken into account.
The results of the mold flow analyses - ideally in 2-3 comparative variations - must be coordinated in detail. For example, an injection point in the visible area and thus a homogeneous filling of the component represents a less serious defect than a distortion in the component resulting from an unfavorably but hidden injection point, which often cannot be brought under control even by adjusting the parameters and tools after the initial sampling.
If the mould flow analyses already reveal strong component distortions, it is essential to determine whether the tool can be "counteracted" by a deliberate change in geometry or whether the component can be homogenized again in terms of wall thickness and designed with geometric flow aids to reduce stresses.
A non-visible connection of housings is optically optimal, but complicates the tool, e.g. through sliders, reduces the cooling surface and thus harbors the risk of component stresses and/or cracking of the housing during drop tests. This also needs to be weighed up and coordinated both in terms of design and tooling.
These aspects must be properly prepared and discussed with the end customer, as they are often not aware of the manufacturing and functional effects in detail.
A final design status can then be created on this jointly agreed basis, which - depending on the scope of the changes - should ideally also be sampled and tested again as a prototype.
Only this data version forms the basis for toolmaking. Change indices and clear "request" and "release" markings on the drawings must be used to ensure that the final data version and not just the request version finds its way into toolmaking.
This detailed coordination between the inquiry and the actual start of tool construction is an aspect that is usually not taken into account in terms of time and cost by either the end customer or the injection moulding partner in the project plan, so that deadline pressure often arises here, which in turn jeopardizes the series maturity and testing of the final solution and thus the quality of the product. Development offices also often underestimate this phase and/or do not understand this budget and the effort involved, as the customer often believes that "the design is already finished" with the first prototype and the initial inquiry data.
Ideally, the company's internal design department and quality assurance department should take over the data at this point at the latest, in order to be able to take over project and quality control during production.
Ideally, the development service providers should remain involved and informed during the initial sampling and the resulting measures. "Pre-releases" of components that actually deviate from the tolerances and geometries defined in the design are critical due to deadline pressure, as experience has shown that this can lead to malfunctions and complaints that often only occur when a large number of products are already on the market....
It is also often neglected to agree on a time window when the remaining points of the "pre-release" are implemented and the actually agreed article condition is produced, as the injection molding manufacturer then has to produce and deliver and cannot remove the tool from the machine. Furthermore, sufficient time should be planned to extensively test the initial samples and subject them to endurance tests, as the prototypes have typically been tested in other manufacturing processes or other materials (RP).
Last but not least, accompanying tests should also be carried out during the ongoing series production process, both at component and assembly level. Material changes due to a lack of availability or even the conversion from 1A raw granulate to recyclate must also not be made simply and out of a misunderstood "sustainability", as these recyclates usually have considerable deviations in the mechanical material properties.
If you take the above-mentioned aspects into account and plan this into the project plan and with regard to the market launch date, you will be spared the saying from the headline... We and our network of injection molding partners will be happy to support you with your plastics projects!
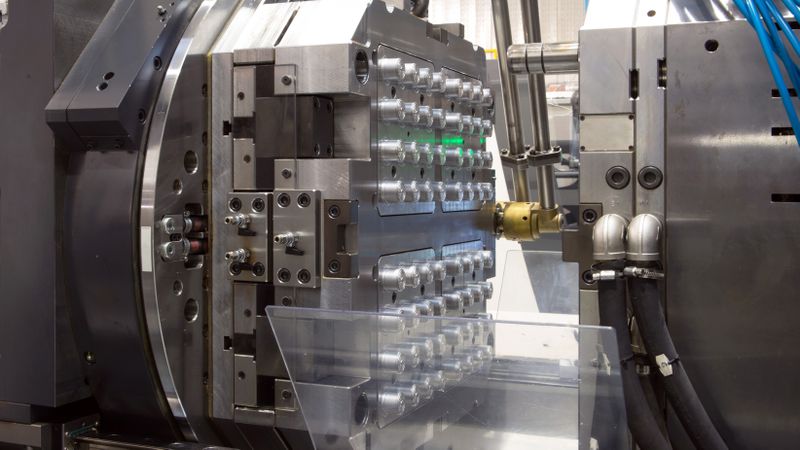
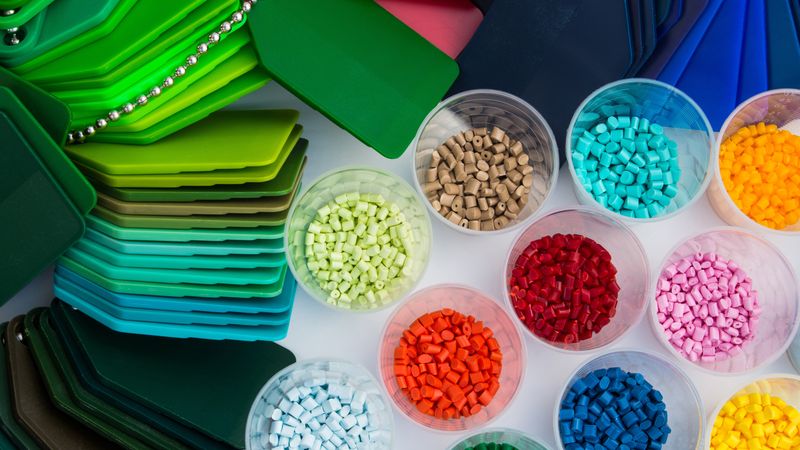
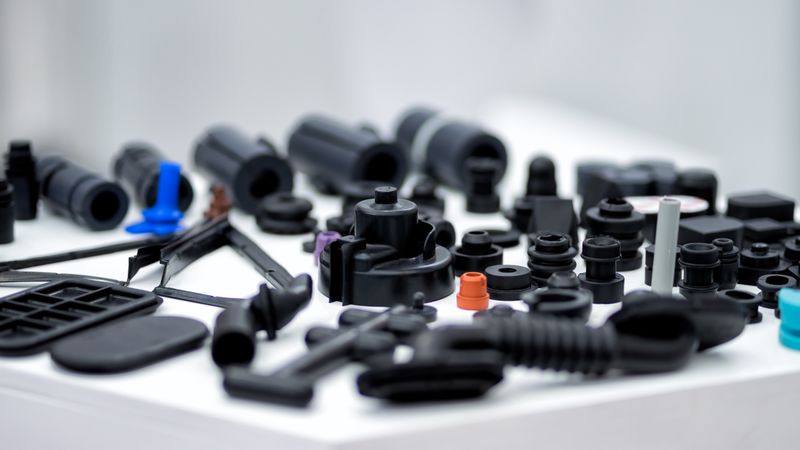
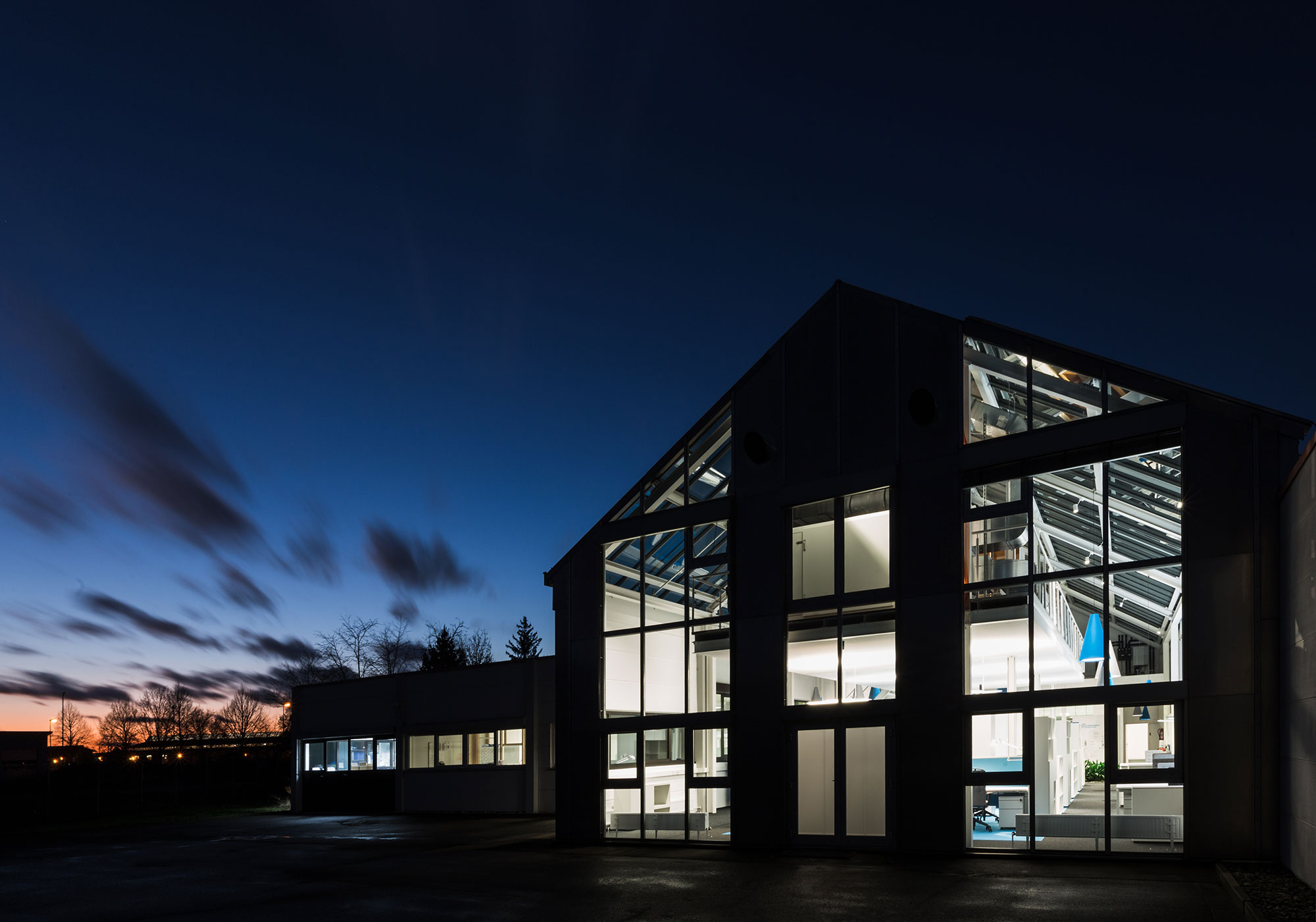