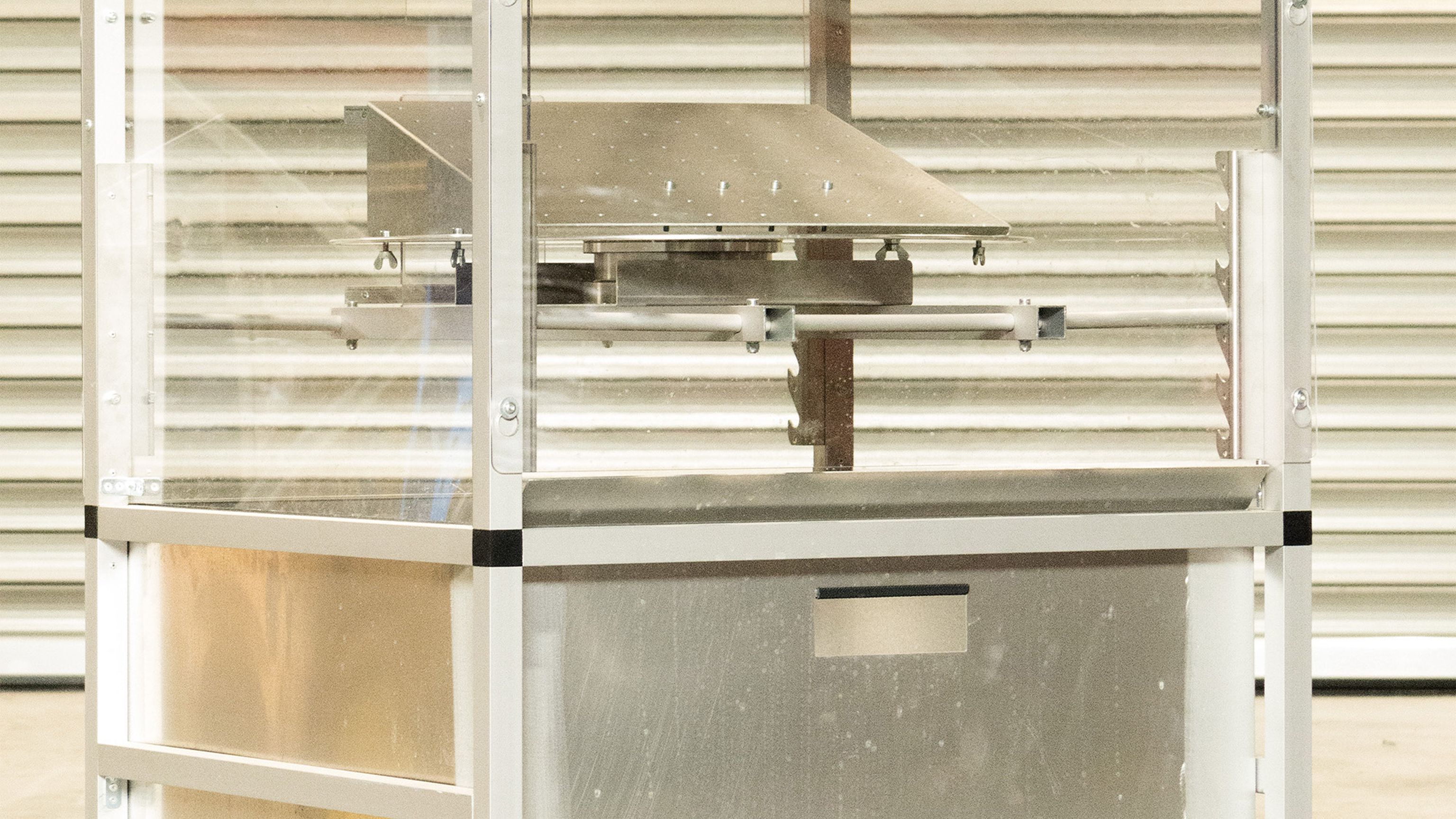
Entwicklungsbegleitende Produkttests
Nachhaltigkeit eines Produktes wird oft nur über die Ökobilanz eines Materials oder seiner Fertigungstechnologie definiert. Die Funktionssicherheit und somit die Langlebigkeit eines Produktes - ob es also nur ca. 3 Jahre oder eben 15 Jahre im Einsatz ist - ist jedoch ein ebenso wichtiger Faktor für die Nachhaltigkeit eines Produktes. Hierfür übernimmt die ausgiebige Validierung eines Produktes im Entwicklungsprozess einen ganz wichtigen Bestandteil.
In den letzten Jahren hat sich im Entwicklungsprozess eines Produktes der zeitliche Anteil für die Validierung und Verifizierung bei vielen Herstellern deutlich reduziert. Dies gründet in immer kürzerer Entwicklungsprozesse und teilweise auch verkürzten Lebenszyklen der Produkte und einer größeren Anzahl an Produktvarianten. Andererseits stieg jedoch zumeist die Komplexität der Produkte und deren Funktionsanforderungen und Miniaturisierung an, was eigentlich einen größeren Anteil für die Validierung zur Folge hätte.
Umso wichtiger ist es aus unserer Sicht, bereits während des Entwicklungsprozesses möglichst frühzeitig erste Indikationen zu essentiellen Produktfunktionen zu erhalten. Zwar kann mittlerweile bereits vieles in Computerprogrammen simuliert werden. Jedoch ist jede Simulation nur so gut wie die Daten und Formeln, die Ihr zugrunde liegen.
Doch gerade, wenn es um die dynamische Beanspruchungen und die Dichtigkeit von Produkten geht, ist der Simulationsaufwand meist recht hoch und kann oft nur einen Teil der späteren realen Belastung darstellen.
Wir bei BUSSE versuchen daher unsere Kunden in diesem Bereich proaktiv zu unterstützen und haben aus diesem Grund einfache Testvorrichtungen zur Validierung von Falltests (Schockabsorption) und Wasserdichtigkeit (IP Schutzklasse) entwickelt und gebaut. Dieses Testequipment ermöglicht es uns bereits frühzeitig mit z.B. Funktionsmustern erste wichtige Indikationen praktisch zu erfassen und in die Konstruktion einfließen zu lassen.
Die Falltests demonstrieren anhand von RP-Modellen oder im Originalmaterial gefrästen Modellen relativ deutlich, welche Stellen am stärksten belastetet sind und wie sich die Bauteile zueinander verschieben. Optimierte Versionen können dann auf die gleiche Weise getestet werden und führen dann oft zu wichtigen weiteren Erkenntnissen, da sich die kinetische Energie nach der Versteifung einer Stelle dann oft an einer anderen Stelle – idealerweise auf mehrere Funktionselemente verteilt – durchschlägt.
Ebenso lassen sich dann Erstmuster im gleichen Testaufbau prüfen und das Verhalten mit den entwicklungsbegleitenden Versuchen vergleichen. Vor allen Dingen beim Einsatz von Rezyklaten oder die Umstellung von Materialien im Produktionsverlauf liefert dies wichtige Erkenntnisse.
Die IP Schutzklasse ist wiederum für nahezu alle elektronischen Produkte von großer Bedeutung, um einerseits die Platinen selbst vor Kurzschlüsse durch Wasserbrücken zwischen stromführenden Komponenten und andererseits den Nutzer vor unkontrollierten Stromschlägen zu schützen. Uns lag dabei eine hohe Flexibilität der Testvorrichtungen am Herzen, um möglichst viele Anforderungen abzudecken und uns gleichzeitig möglichst nahe an den Normvorgaben zu bewegen. Daher haben wir hier eine einfache Testkammmer erstellt. Die von mehreren Seiten entsprechend der IP-Klassifizierung eine Beregnung ermöglicht.
Für viele Kunden-Projekte haben wir weitere projektbegleitende Testvorrichtungen erstellt (z.B. Schubladen-Auszugstest oder Förderanlagen-Prüfstände) um das Verhalten unter Dauerlast und die Verschleißeffekte im gesamten Lebenszyklus zu simulieren.
Natürlich sind diese Testvorrichtungen nicht mit denen von akkreditierten Prüfinstituten zu vergleichen, bieten uns und unsere Kunden jedoch eine schnelle und kostengünstige Möglichkeit, frühzeitig praktische Erkenntnisse und erste Validierungen durchzuführen und in den Entwicklungsprozess einfließen zu lassen.
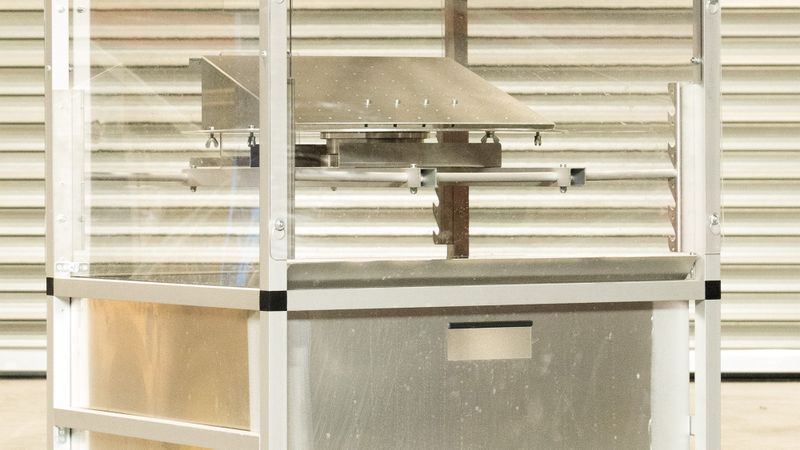
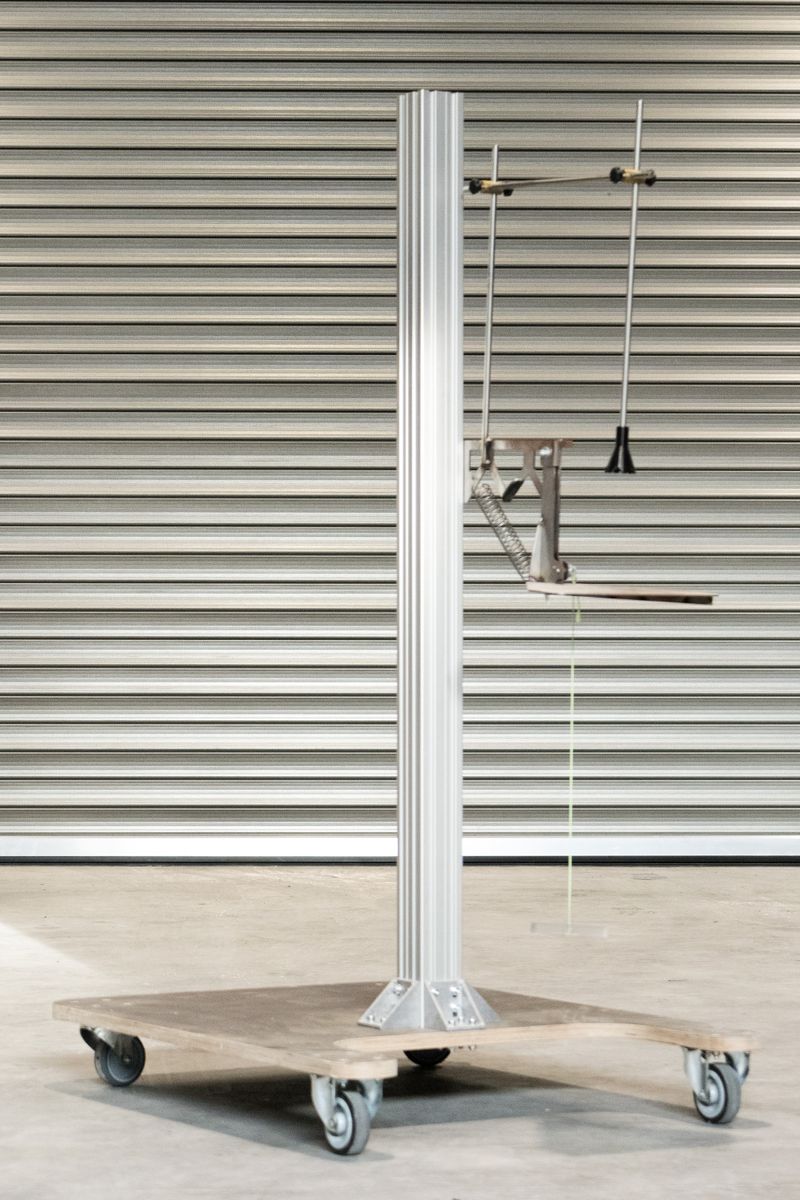
Unsere Kompetenz wird nicht nur durch 400+ Auszeichnungen belegt, sondern auch durch die Begeisterung unserer Kunden.
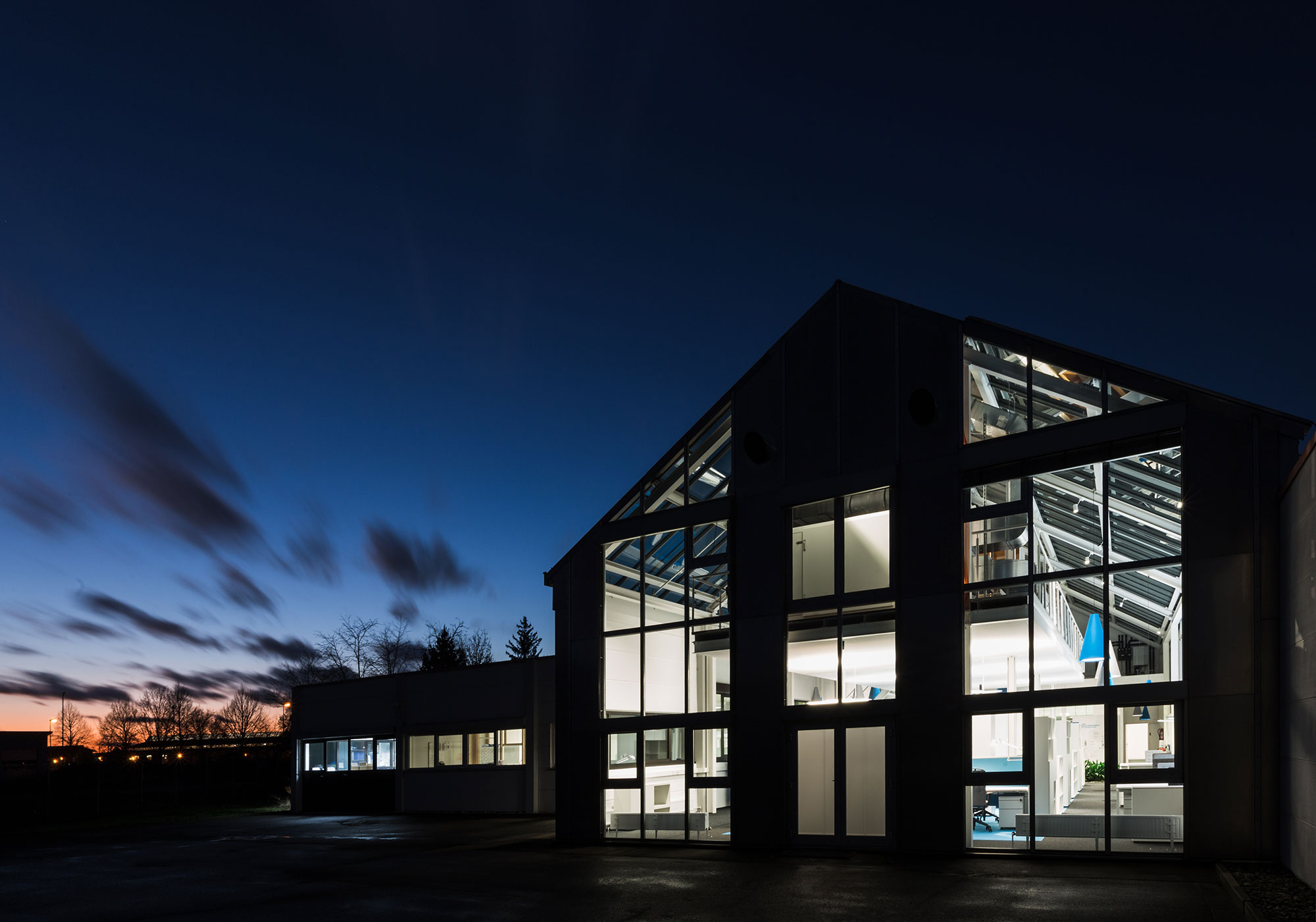